Conveyor systems are found in dozens of industries. They move large numbers of finished goods, raw materials, and components in production and assembly lines, deliver baggage in airports, and transport parcels and packages in warehouses and distribution centres. They’re efficient, fast, and reliable, reducing the likelihood of product damage and the numerous risks facing manual material handling.
The Basics of Conveyor Systems
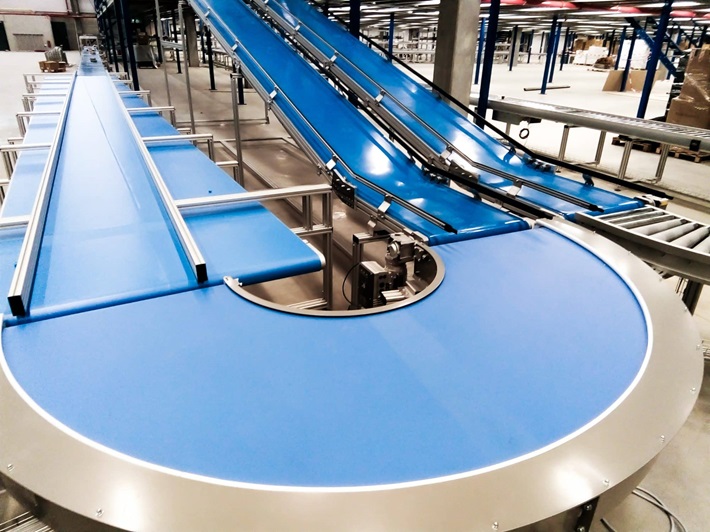
In their most basic form, conveyors are mechanical devices used in uninterrupted material handling. They move goods and products from one point to another in a continuous flow, often within the same facility and play a vital role in workplace productivity and safety. Conveyor systems come in different forms and layouts, with belt and roller types the most common. What’s important though is that different systems can be configured to meet specific company and industry needs. Their ability to move any load, and to varying lengths or heights makes them extremely popular in many businesses.
Types of Conveyors
There are dozens of conveyor systems, but the most common include belt, roller, slat and overhead conveyors. Belt conveyors are the simplest and most widespread, and consist of rubber or polymer belts supported by a frame comprised of moving rollers. Belt conveyors are seen in supermarket checkouts, mail rooms, and manufacturing plants and warehouses dealing with lighter goods.
Roller systems come as gravity or motorised roller conveyors. Gravity conveyors are some of the most economical types, consisting of rollers or skate rails mounted in a frame. They’re installed at an angle and use gravity to move goods. Motorised systems are similar but have motors mounted after a specified number of rollers. These are used to move larger and heavier items. Both types are configurable for a variety of settings, and motorised types can also feature sensors to prevent loaded items and materials from bundling together.
Slat conveyors use slats connected by a chain. The slats are made of stainless steel, aluminium or plastics and feature a smooth, flat surface ideal for moving fragile items. The conveyors are often found in the food, beverage and pharmaceutical industries and benefit from easy maintenance (individual slats are simple to replace) and durability.
Overhead systems are designed with efficiency in mind and to free up floor space. They grip products and materials from above and move them down the line. Enclosed, open-track and chain conveyor systems are some of the more common types. You’ll see these in bottling plants and assembly lines.
How They Work
Conveyor systems are configured as a closed loop, consisting of a series of driven and auxiliary pulleys, along which belts, rollers or slats are placed. Drive pulleys often feature motors running on AC power, and are usually located at the discharge end. Idler and tail pulleys guide the belts or slats and create the required tension in the system. Belt cleaners also remove materials attached to belts or slats after the discharge point.
Benefits These Systems Provide
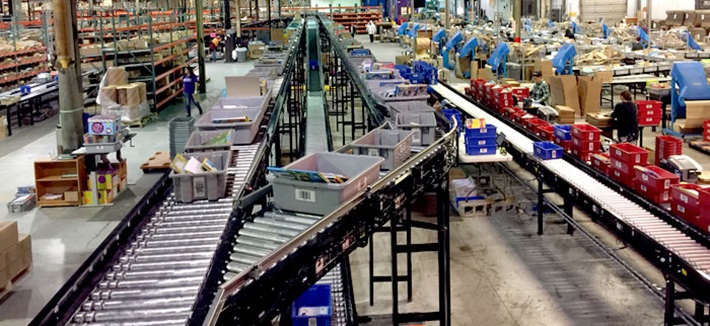
- The acceptance of conveyors in industries as diverse as manufacturing, general material handling, construction and mining all stem from the long list of benefits they provide:
- Adaptability – modular designs expand the scope of applications, as well as the flexibility for efficient transport of goods in varying settings. The systems can be assembled on-site, and modified to meet specific business needs. They also can be incorporated into existing material handling operations.
- High volumes and continuous operation- simple layouts and dependability mean systems can move products of any size or weight continuously. Productivity is also increased, with materials transported without unnecessary downtime.
- Reduced costs and increased safety- cutting out the need for manual material handling reduces labour costs, the likelihood of injuries or fatigue, and any chances of human error leading to damage to property or inventory. Conveyors can also be specified to meet specific industry safety regulations and procedures, such as in warehousing and other areas.
- Increased control and automation – current conveyor systems can be configured for moving items at specified speeds, helping in quality control and detection of faulty items, as well as the ability to move backward or forward, such as in automated assembly lines. Unloading is also simplified, without the need for manual labour.
- Low maintenance – even larger motorised systems only need periodic maintenance to work at their full potential. Moreover, simpler layouts like gravity conveyors are virtually maintenance-free once installed.
Where Conveyors are Used
The flexibility, speed, efficiency, and high safety in everyday tasks like material handling, general storage, manufacturing and assembly make conveyors indispensable in hundreds of businesses. This includes moving raw and building materials in mining and construction sites, simplifying operations in food and beverage production and packaging, baggage handling at airports, transporting waste products in recycling plants, general warehousing, transport and distribution, increasing quality control in the pharmaceutical and cosmetics industries and so much more.
Systems come in several basic types that are easily adapted to company needs in terms of volume, floorspace and budgets, while proving highly beneficial in reducing overall cost and increasing workplace safety.