Serious performance upgrades begin with the engine internals. The pistons and connecting rods are some of the most tortured mechanical parts there are, but what is often overlooked is what connects them. Humble piston pins may not be worth mentioning, but this is the missing link in getting all that power down to the wheels. When upgrading pistons and conrods, it only makes sense to also upgrade what connects them, and a piston pin of higher quality materials or thicker wall thickness is the way to go.
What are Piston Pins?
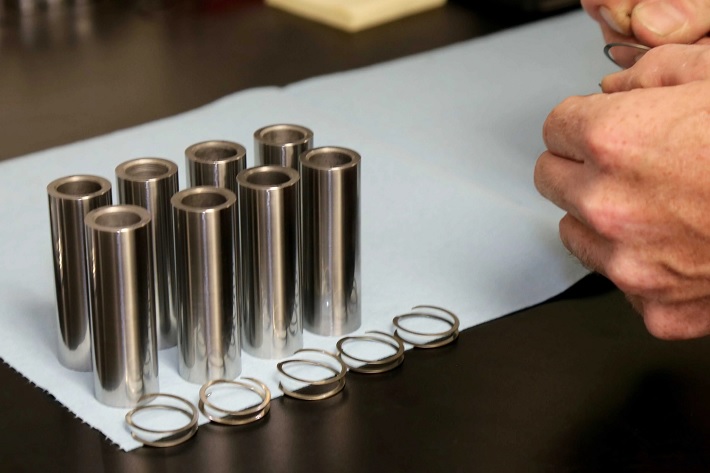
Let’s get all the terminology out of the way first. Piston pins also go by ‘wrist’ or ‘gudgeon’ pins and are the metal parts that connect the piston to the connecting rod. A piston gudgeon pin slots into the appropriately named wrist pin boss, a hollowed-out section in the piston skirt to accommodate the top end on the conrod. They take a pivotal role in how an engine works, tasked with providing bearing support for the conrod as it is pushed down into the cylinder head by the extreme forces acting on the piston and piston crown. Piston pins can take the form of both solid or hollow cylindrical rods, and come in different materials and coatings that determine overall strength. A major factor here is also wall thickness, but also weight. These need to be balanced for the characteristics of the engine, and the modifications were already done to pistons and conrods.
Matching parts of the same quality and properties means you get a balanced engine. Retailers in the know largely cut out the work for you when you’re after higher horsepower and torque figures, and piston pins are often packaged with pistons of the same quality. Alternatively, you can buy them separately, and opt for higher quality to prevent any chances of pin failure. If this does happen, the chances of catastrophic engine failure and the piston seizing are extremely likely.
Piston Pin Types
A piston gudgeon pin can be sourced in three different variants – fixed, floating, and semi-floating depending on how it fits and pivots within the piston wrist boss. Fixed pins also go by the name of anchored piston pins and they pivot freely in the top end of the conrod, connected to the piston skirt by way of bushings. The piston locks the pin in place with screws that go through the pin bosses. You’ll rarely find these as viable performance variants due to the increased friction and wear.
Semi-floating piston pins have chamfered ends to allow the pins to move freely within the piston boss bearings. They are secured to the midsection section of the conrod by press-fitting and a method largely found in production cars.
Floating gudgeon pins float freely both in the piston bosses and the connecting rod top end. The connection is made by use of spring-loaded locks called circlips and buttons on either end of the bosses centre the pin into the optimal position. The benefit here is the even distribution of loads during each phase of the combustion cycle and the ability for adjustment and removal. This is the preferred pin type when looking for a performance upgrade.
Sourcing New Piston Pins – What to Look For
The choice of materials the pins are made of determines how they perform and how long they will last. Pins in production cars are steel offerings, with surfaces that are hardened to improve wear resistance. Hardening the pin can take two forms- case hardening, or what is known as carburising, The other is nitride hardening, which is also used in strengthening modified crankshafts. Both methods help with the compressive stresses the pins endure, thus reducing the risk of piston pin fatigue and possible ruptures. Strengthened steel alloys (H13 tool steel, 300M, 9310) can also undergo hardening to reach exceptional strength. Stress tests against standardised hardness scales (Rockwell) ensure the pins will last at all loads.
Wear resistance is improved with coatings. DLC or diamond-like coatings have been used for over a decade in motorsports, and are recommended for any upgrade to engine internals.
Besides steel, pins in high-end variants are made from nitride-treated titanium and DLC coatings that benefit from low weight. These are preferred in high-revving engines. Recent advancements in racing engine technologies have led to pins with aluminium beryllium inner sleeves and coated steel outers.
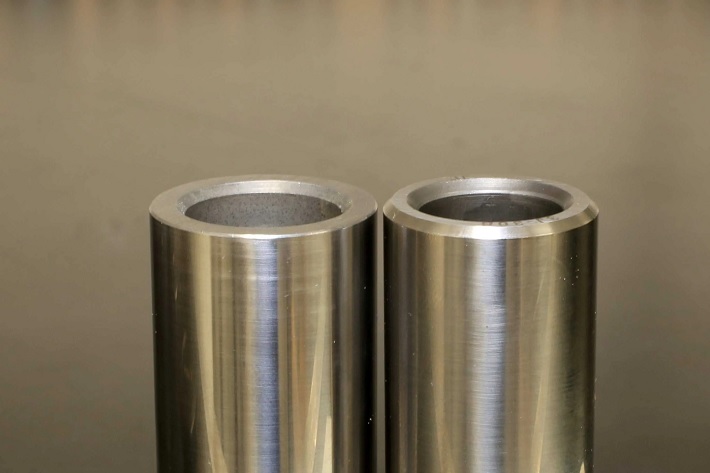
Piston Pin Thickness
Wall thicknesses depend on the loads and applications. Generally, the higher the performance requirements the thicker the piston pin wall. These are specified in inches and typical sizes used in upgrades to stock engines are 0.200″ and 0.250″. This is good for modified engines rated at over 1000bhp. By comparison, the wall thickness in standard production cars hovers at 0.100″ or less than half of performance variants. With higher thickness comes more weight, but the choice of materials, especially alloys, helps in this regard. What is crucial is balancing the weight in the piston and conrod assembly (and taking into account the weight of the piston pin) to provide smooth power delivery.